Pros and cons of using industrial robots in your manufacturing operation
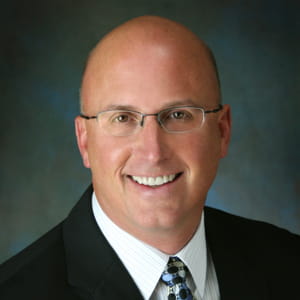
Today’s industrial robots work in a wide range of automated industries, from semiconductors and automobiles to plastics processing and metal forging. Pretty much any repetitive operation is a great job for a robot, particularly if it’s dangerous or difficult for people. Robotic process automation is transforming manufacturing.
The application of robotics in manufacturing industries is particularly valuable. Manufacturing robots have been used for high-volume processes, but as the technology advances and the cost of industrial robots decline, more options and opportunities are opening for medium- and small-sized operations to leverage robot manufacturing.
At the same time, these robots are helping manufacturers address many of the key challenges they face, including tight labor pools, global market competitiveness and safety. Robotics and manufacturing are becoming increasingly intertwined, with robotics integration enabling more flexible automation.
If you’re curious whether robots can enhance your value stream, here are the main pros and cons to consider when it comes to industrial automation and robotics:
Advantages of industrial robots
1. Better quality control and consistency
Along with other tech — such as the industrial internet of things (IIoT), artificial intelligence, data analytics or 3D printing robots — industrial robots are able to provide better production quality and more precise and reliable processes. Added benefits also include reduced cycle times and real-time monitoring to improve preventive maintenance practices.
2. Maximum productivity and throughput
An industrial robot increases speed for manufacturing processes, in part by operating 24/7. Robots don’t need breaks or shift changes. The speed and dependability of robots ultimately reduces cycle time and maximizes throughput. Robotic factory automation and manufacturing with robotics enables high efficiency.
3. Greater safety
Using robots for repetitive tasks means fewer risks of injury for workers, especially when manufacturing has to take place under hostile conditions. In addition, supervisors can oversee the process online or through remote monitoring from a remote location.
4. Reduced direct labor costs
The cost of having a person handle many manufacturing operations is often more expensive than a robot. This can also free up workers so their skills and expertise can be used in other business areas, such as engineering, programming and maintenance of the robotics used in manufacturing.
5. Keeping manufacturing in the U.S.
Some argue that robots are taking jobs away from U.S. workers, but that’s not necessarily the case. Industrial robots there are typically integrated into a series of operations that require human expertise. For example, you could have a robot welding parts that are handed off to a person to perform a task that requires a human’s intuitive "if, then" thinking. The future of robotics in manufacturing involves humans and robots working in factories together.
Disadvantages of industrial robots
1. High initial investment
Robots typically require a large upfront investment. As you research your business case for purchasing, consider all the costs of industrial robots, including installation and configuration. You should also evaluate whether your robot can be easily modified if you need to alter operation in the future. Robotics for manufacturing is a significant investment.
2. Expertise can be scarce
Industrial robots need sophisticated operation, maintenance and programming from controls engineers. While the number of people with these skills are growing, it’s currently limited. As a result, it’s important to consider the personnel investment you’ll need to make to bring in that expertise or “retool” your existing staff to take on the task of working with robots in industrial automation.
3. Ongoing costs
While industrial robots may reduce some manufacturing labor costs, they do come with their own ongoing expenses, such as maintenance. In addition, you’ll want to consider the costs to keep your robot and any related IIoT-connected devices protected from cyberthreats.
Getting started with industrial robots
Interested in learning more about the types of industrial robots that would benefit your manufacturing business, from collaborative robots to six-axis robotic arms to autonomous robotics?
If you’re ready to explore options for robotics in industry, contact Wipfli to request a complimentary consultation on how robots and manufacturing can work together for your business, from material handling to assembly processing to pick-and-place tasks. We’ll discuss how automated technology, vision systems, precision control, AC servo motors, cobots and other digital solutions can take your production processes and inventory management to the next level as part of Industry 4.0 and the future of factory robotics.
Sign up to receive additional manufacturing content in your inbox, or continue reading on: