13 ways manufacturers can build capabilities to enable growth
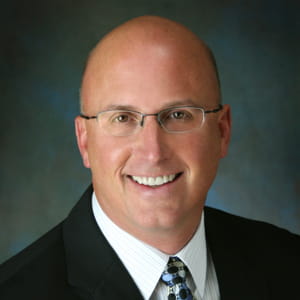
In a Wipfli study of nearly 200 manufacturers, a majority of respondents noted that current production capacity is less than 80% of designed capacity. The same survey found that respondents are not planning to pursue many opportunities for growth over the next three to five years. This hesitation highlights the need for digital transformation in the manufacturing industry to drive efficiency and growth.
There are many reasons why manufacturers are opting to table growth right now, but the well-documented labor shortage is unquestionably a primary factor. The challenge of finding and retaining qualified staff is forcing many businesses to turn down new work and even disengage from existing customer relationships. This situation underscores the importance of digital transformation for manufacturing companies to overcome these challenges and improve operational efficiency.
The super-tight labor market can no longer be chalked up to a trend. It’s the new reality, at least for the foreseeable future. But there are alternatives to doing more with less. Explore these 13 practical and highly effective ways manufacturers can build the workforce and the capabilities they need to support their growth and expansion strategy, leveraging digital transformation and automation in manufacturing.
Nontraditional recruitment strategies for workforce transformation
Traditional recruitment avenues are coming up short. Here are five methods manufacturers are using to expand the talent pool and support manufacturing growth:
- Look to adjacent industries, like hospitality: Hospitality workers are generally not well-compensated, and the sector was hit hard by the COVID-19 pandemic. Manufacturers that make a compelling case for the higher pay and greater stability offered by their industry could tap into a labor pool that is already attuned to service and collaboration.
- Become a second-chance employer: Individuals with a criminal record face many barriers to employment. Second-chance hiring opens up access to an often overlooked source of talent while giving these people a chance to make a good living.
- Offer friends-and-family referral bonuses: Companies are quick to give recruiting bonuses to new hires. But the recruits who stay the longest are typically friends or family of existing employees. So why not offer a referral bonus to the people who are helping you find talent that is more likely to stick around? It may result in a higher payout on the front end — but turnover costs more in the long run.
- Add daycare to your benefits package: There is a share of the workforce that stays home after having children because of a lack of affordable daycare. More companies are responding by offering daycare benefits, even to part-time workers. It’s a creative way to remove barriers, both for people who want to work and for employers who need more people.
- Consider job sharing opportunities: Not everyone wants to work full time, so more manufacturers are turning to job sharing. In this scenario, two employees who want to work part time form a unit and work alternate days. In return, manufacturers can cover an entire shift.
Upskilling and job paths for digital manufacturing transformation
Finding talent isn’t the only hurdle to growth. According to Wipfli’s survey of manufacturers, a majority of respondents reported that they are grappling with innovation skills gaps. Across the manufacturing sector, competitiveness will increasingly hinge on having a workforce that can run complicated and digitized operations
There is a retention component to this, as well. Learning new skills can be intimidating. Training conducted in a way that alleviates frustration will reduce the potential for staff to become discouraged and leave. Leverage these three tips for skill development in the era of digital manufacturing operations:
- Use accelerated learning labs: Traditional training methods have relied on one employee looking over the shoulder of another during the workday. It’s typically unstructured and stressful. Accelerated learning labs take the stress out of the situation by enabling employees to learn independently, away from the line. Employees can build a solid foundation of knowledge before they start hands-on training, enhancing their digital skills for the manufacturing industry.
- Employ augmented reality (AR): The use of AR for training goes hand in hand with accelerated learning labs. This technology overlays real-world environments with interactive graphics. Because employees can work through real-world training modules on their own, it’s a more efficient and less disruptive way to build the workforce of tomorrow, supporting the digital transformation in industrial manufacturing.
- Incentivize training with pay-for-what-you-know: One sure-fire way to grow a highly skilled workforce is to incentivize training with pay-for-what-you-know. Employees can increase their pay for every new capability or skillset they learn. You’ll have greater employee buy-in for building a digital-ready workforce and more flexibility for managing day-to-day workflow. Likewise, employees who have more control over their job paths and the opportunity to earn higher pay will be more inclined to stay, contributing to overall productivity and innovation.
Automation, cobots and workflow technologies for manufacturing transformation
Employees tend to feel threatened by automation and other Industry 4.0 capabilities, but this is not about replacing humans. It’s about building capabilities to enable growth through digital transformation. Manufacturers that are chronically short-staffed should target difficult-to-fill positions that require highly skilled but hard-to-find specialists, as well as jobs that are monotonous, repetitive, dirty or pose a safety risk.
The best part? The return on investment for many of these strategies is three to five months. Here are five tips to get started with automation and digital transformation for manufacturers:
- Invest in welding with smart tables: Welders are one of the most difficult, highly skilled trades to fill. To get around this, manufacturers are investing in robotic welders and, more specifically, tabletop welders with smart tables. With this technology, welding robots can be programmed in a matter of minutes, and they don’t require previous automation or programming experience. An employee with limited experience — someone recruited from the hospitality industry, for example — could be running one of these cells with a few hours of training, showcasing the benefits of digital transformation in manufacturing.
- Automate repetitive activities: Repetitive activities like pick-and-place and checking-and-counting are ripe for automation. Robots can more efficiently fulfill orders because they don’t require breaks, and vision sensors can more quickly and accurately check and sort items than humans. Employees can be redeployed to more solution-oriented work where they are likely to experience greater job satisfaction. This integration of robotics and artificial intelligence improves overall efficiency and productivity.
- Add cobots to your team: Cobots are designed to assist people with everything from minor operations — such as picking and presenting parts to a human — to handling operations that pose a safety risk. Humans can focus on higher-order work, while their cobots can handle repetitive, monotonous or lower-value tasks. This collaboration between humans and machines is a key aspect of the digital workplace for manufacturing.
- Streamline workflows: Disruption is the new reality for manufacturers. Workforce automation technology enables companies to adapt workflows with ease. Experiencing a high rate of absenteeism? Instead of relying on shift supervisors to redeploy your available workforce, the technology can match skills and capabilities with job orders before the shift even begins. This use of data analytics and Internet of Things (IoT) contributes to improved operational efficiency.
- Implement robotic process automation (RPA): The shop floor isn't the only place where manufacturers are struggling to find people. Back-office positions are also going unfilled. RPA automates rules-based business processes, such as accounts receivable tasks, enabling manufacturers to accomplish more with fewer people. This is another example of how digital transformation in manufacturing can enhance productivity across various departments.
Build a smarter strategy to enable growth through digital transformation
It’s true that revamping long-established processes is complicated under the best of circumstances. It’s even more so when you are facing disruption on so many fronts. However, uncertainty is the new normal. Manufacturing leaders who act now to build up their workforce and expand their Industry 4.0 technologies will be better positioned to weather disruption and seize opportunity.
Wipfli's manufacturing and technology advisors can help you identify and prioritize both quick wins and long-term strategies to build your digital capabilities. With more than 90 years of experience helping manufacturers, we understand the hurdles you need to clear — and the most overlooked means for achieving growth. Learn more about how the Wipfli team can help you get the most from your manufacturing organization and guide you through the digital transformation process, addressing challenges such as legacy systems integration and cybersecurity.
Next up, we’ll explore best practices for assessing merger and acquisition opportunities. Don’t miss out on that and our other thought-provoking articles just for manufacturing leaders. Sign up using the form on the righthand side of this page to receive articles and our manufacturing newsletter directly in your inbox.
Related content: