How manufacturers can improve information flow
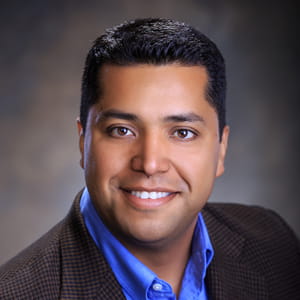
The way that information flows throughout a manufacturing business is a major factor in how efficiently the business runs. If you’re looking to improve information flow, the best way to ensure success is by taking a deliberate approach.
Step one: Assess your current information flow
The first step is to conduct an honest assessment of your current state of affairs.
Keep in mind that information flow naturally deteriorates, so it needs to be monitored and maintained. It’s common for this to occur in organizations that are growing or where turnover has occurred. People may incorrectly assume that new employees are going to immediately understand the information flow when they step into their new roles. As a result, flow suffers, which is why it’s critical to constantly monitor and sustain it.
Process mapping is a good way to identify problems with information flow. Since information is invisible, it’s useful to physically walk the flow. Take a look at the value stream you’re going to follow, identify its goals and then see how that matches up to reality. Go from station to station and person to person. Inevitably, you’re going to find redundancies and unnecessary back and forth in the information flow.
Remember that people who work on the shop floor are a valuable source of knowledge. Often, flow is examined from the perspective of someone high in the company, such as upper management. But you’re able to learn a lot from people on the shop floor.
Employees on the ground often work around processes due to missing or incomplete information. For example, at one company, sales personnel were contributing to an increase in activity at the company’s own call center because they needed information about the status of claims. Physically tracking the flow helps unearth issues like that.
Step two: Take action on your findings
Once you’ve worked through the value stream mapping exercise, you’re ready to start tackling specific problems.
One common problem is that employees on the shop floor often don’t understand the reasoning behind their tasks or the communication flow that must occur to support their actions. You’ll have a very different conversation if you speak with someone who understands how the business works behind the scenes as opposed to someone who only understands how their machine works.
To help ensure everyone is on the same page, you can use portals that provide visibility into information flow. People need to be able to relate to their work to be as effective as possible. That’s not going to happen if they don’t see how they fit into the overall structure of the organization. Understanding the big picture allows information to flow better.
Before you start to put together a technical system, the key is to envision the process in the abstract. What information is necessary to accomplish your goals, and what’s irrelevant? Lay out a roadmap for those goals before you implement technology to automate processes.
Identify the information that’s necessary at each step of the process. There’s a tendency to want to capture a lot of data, but that’s often unnecessary. A good filter for determining whether information should be captured is to ask how fast the recipient is going to consume it. If the answer isn’t right away, it probably shouldn’t be a priority.
Start with the minimal pieces of information necessary, and then expand later. It’s easier to start small and expand than it is to trim down. Empower your employees to provide information about inefficiencies and ways to improve the workflow. Set up a feedback loop to ensure that information is flowing both ways and helping to facilitate continuous improvement.
Ultimately, information flow should be improved by training employees so they understand the value-stream map and feedback loops. Feedback loops allow you to continually refine processes, products and services. Empowering employees so they’re able to make improvements based on this information goes a long way to creating and supporting the right information flow.
Getting help to improve information flow in business
Wipfli has experience improving information flow in organizations and can assist your manufacturing business with assessing your current information flow, performing process mapping and value stream mapping, and creating a new information flow model. Contact us to learn more.
Sign up to receive additional manufacturing content in your inbox, or continue reading on:
- How automation can lead to more loyal customers — and employees
- The Gemba Walk: a tried and true strategy for improving employee retention
- How manufacturers can protect their supply chain in times of crisis
- Manufacturers can find recruitment opportunities through and beyond the COVID-19 crisis, and here’s how