Are you looking in the right places for automated manufacturing opportunities?
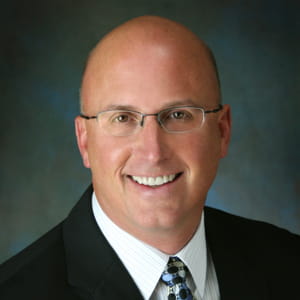
The words “automation” and “manufacturing” tend to conjure images of industrial robots assembling vehicles with rapid precision or robots working side-by-side with their human counterparts.
Robots may be the most instantly recognized hallmark of smart factories and Industry 4.0. But they are only one component of a broad array of automation technologies that are available to manufacturers. And they aren’t always the right place to start when making the transition to an automated shop.
In fact, some of the best, most straightforward opportunities to remove effort, improve accuracy and reduce risk are fairly mundane. Automating information flows or manual production processes may lack the wow factor of a robot, but you could leapfrog ahead of your competition in terms of efficiencies gained.
Here’s how to make sure you’re looking in the right places for automation opportunities that will deliver the results you want.
First define the “what” of automated manufacturing
The field of automation is evolving so fast that it’s easy to get enamored with the latest robotic apparatus or industrial internet of things (IIoT) capabilities. However, before you implement the next-generation mobile manipulator or transport drone, you need to first identify what it is that you want or need to accomplish. There are a host of reasons to automate, including:
- Increase throughput: Digital workflows and automation technologies simply get the job done faster. Moreover, robots, artificial intelligence (AI) and other Industry 4.0 capabilities don’t require breaks, enabling manufacturers to expand the workday — and their capacity — without significantly adding to their payroll.
- Improve accuracy: Every manual touchpoint introduces the potential for error. Automation provides for greater precision and consistency by removing that potential from the equation.
- Reduce risk of injuries: Even with air-tight safety measures in place, shop floors can be dangerous. Robots and cobots can handle tasks that are ripe for injury, whether from repetitive actions, difficult maneuvers or heavy or dangerous equipment or materials.
- Gain competitive insights: Manufacturers that don’t know what they don’t know about their equipment, processes and even their customers are leaving value on the table. Sensors, AI and analytics software can unlock prized insights that can be used to build a significant competitive advantage.
- Mitigate labor shortages: Skilled and unskilled talent is still in high demand — and difficult to come by. Automation can enable manufacturers to do more with fewer resources. It can also double as a tool for recruitment by attracting digital natives and “techies” who enjoy working with industrial technologies.
Then identify the “how” of automated manufacturing
After defining what you want to achieve, you can build the case for how and where to invest in automation. In doing this work, you may be surprised to find that the opportunities with the best and fastest return for investment are relatively low profile or not on the shop floor at all.
Some of the best places to start include:
- Repetitive and labor-intensive tasks: The most valuable asset that people bring to the job is their brain. Far from replacing people, automation can enable employees to trade out repetitive or boring tasks for more challenging, problem-solving roles. Ultimately, this is a better use of their talent and your capital.
Or consider tasks that no one wants, like counting inventory. Instead of assigning a person to hand count materials, you can deploy drones and sensors to collect this information, which can then be tracked in your enterprise resource planning (ERP) system.
- Positions that are difficult to fill: While manufacturers are challenged by a tight labor pool overall, some positions, such as welders, are more difficult to fill than others. Rather than risk missed production goals because of a skilled talent shortfall, automate these positions and focus your recruitment efforts in other, higher value areas.
- Business functions with high overhead: Back-office functions, including human resources and accounts receivable, are foundational to the business, but they also consume overhead. Investing in robotic process automation (RPA) solutions to automate manual processes will enable employees to accomplish more in a day with fewer errors and at less cost.
- Paper-based processes: Operations that rely on paper-based processes to run the production floor lose a staggering amount of time to manual entry, lost files, missing information and general errors. Upgrading your ERP or investing in ERP apps to digitize information flow will enable your team to reclaim days, if not weeks, of production time while reducing variances and unplanned downtime.
- Processes that rely on tribal knowledge: It’s not unusual for manufacturers to lean on tribal knowledge in place of defined processes or hard data. Yet, in addition to the inherent risks this poses to business continuity, it can also become a roadblock to productivity and profitability.
Combining business intelligence tools and IIoT capabilities to capture, aggregate and analyze disparate data will lead to faster, more informed decisions. For example, you could generate more accurate quotes that won’t leave your jobs under water or develop production schedules that make the best use of capacity and people.
Always think strategically
Automation can generate tremendous advantages, but there is a caveat. To optimize your investment, you need to create an enterprise-level plan. Automating a cell or a line or a business process alone may deliver some benefits, but they will be limited at best. At worst, piecemeal efforts could hamper operations and create bottlenecks.
To avoid this, you need to first perfect your manual processes. Automating wasteful steps or non-value-added tasks won’t deliver on your goals. It will only waste time at a faster pace. After you have streamlined workflows, you can look across the organization to identify where to best improve on your processes with technology. Opportunities to automate across functions, such as by deploying a robot that can move across multiple cells, will deliver greater efficiencies.
Remember to start small, test, modify and adapt before scaling your solutions. Get it right before going big will save on capital, minimize disruption and build credibility among your staff. And get your employees involved in the process. Show them that you are not replacing them, but rather creating opportunities to use their skills more effectively in support of shared growth.
Not sure where to begin or if you’re getting the most value from your current technologies? Wipfli can help. Our manufacturing experts bring a wealth of experience with helping manufacturers of all sizes plan and execute digital transformation strategies to optimize their operations.
Learn more about how the Wipfli team can help you get the most from automation technologies.
Next up, we’ll look at data: how to collect it and what to do with it. Don’t miss out on that and our other thought-provoking articles just for manufacturing leaders. Sign up using the form on the righthand side of this page to receive articles and our manufacturing newsletter directly in your inbox.
Related content: