New tools for the trades: Technology can help construction firms navigate change and disruption
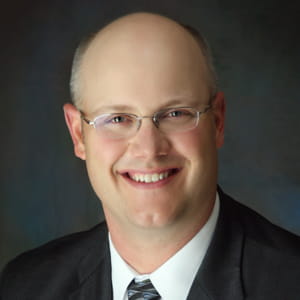
Labor is tough to find, material prices are high and delivery schedules are hard to predict or control. Can we get an app for that? Or, better yet, an “easy button?”
Actually, maybe.
Construction firms haven’t hit digital transformation at full speed yet. As an industry, it’s teetering somewhere around Industry 2.0, whereas manufacturers and retailers are playing with Industry 4.0 plans and beyond. On the bright side, that means technologies and use cases have been fully developed and tested. Now, construction firms can dive right into the right technologies.
Promising tools
Within construction, these innovations show the most promising returns:
1. Blockchain
Put simply, blockchain is a system for recording information. It’s best-known for tracking cryptocurrency transactions, but every industry and business can benefit from having a secure, immutable “source of truth.” Construction firms can leverage blockchain to ensure project information is always accurate, accessible and protected, and that every superintendent, subcontractor and tradesperson is working from the same game plan. Blockchain can eliminate questions about who’s working on what, when. And it retains project records and final documentation.
2. Building information modeling (BIM) and the Internet of Things (IoT)
3D and 4D modeling can help construction firms anticipate challenges and stay on track, both budget- and timewise. A “digital twin” of the physical site can capture and store virtual design during construction and retain information throughout a facility’s lifecycle for future review, analysis and walkthrough.
BIM can be paired with IoT enabled systems and can be leveraged in service and maintenance work, creating potential new revenue streams. For example, IoT solutions can track wear and tear on building systems (e.g., HVAC, electrical or elevators), so maintenance tasks can be activated based on actual usage trends or safety and service-related data points. By deploying smart, data-based predictive and preventive maintenance, construction firms can prevent costly downtime and repairs for their customers — and collect monthly service revenues.
3. Drones
Camera-equipped drones can improve mapping and surveying, job site surveillance and even security. Drones can monitor sites and equipment to support progress reports and inspections, but from safer or off-site locations. And those hard-to-reach nooks and crannies? A digital twin can show you what something should look like or how something should be performing (as noted above); a drone may be able to show you real time what’s going on in those hard-to-reach places.
4. Mobile technology
With mobile applications, construction companies can move business processes out of the office and into the field. Workers save time (and money) when they can punch in, check in and close out projects without coming back to an office. Smart, location-based dispatching can get materials and crews to sites sooner. Scanners can help crew leaders track time and material usage more accurately. And automated invoicing tools can help the firm collect cash sooner and with less effort.
5. Prefabrication
Firms that have space can move major construction tasks out of the elements and into more-controlled indoor locations, which keeps projects on schedule. Multiple steps can be completed near simultaneously, too. For example, electrical and HVAC work can be integrated and fabricated in a warehouse together, then delivered to the project site. Having trades work together, or within closer proximity, can improve coordination and reduce timelines.
6. Wearables
Construction workers are accustomed to PPE. Now, it can work harder (and smarter) to keep them safe. Smart boots, hard hats and gloves can warn workers when they’re at risk of injury, either from fatigue, temperature or incoming equipment. In warehouse or manufacturing’s settings, wearable sensors can also identify opportunities to improve efficiency. Eliminating the number of steps — or minutes — to get materials and tools can add up.
Picking the right tool for the job
It’s easy to get caught up in shiny, new technologies. But not every innovation is a good investment for your firm. Every construction business needs a technology roadmap, just like it needs building plans, detail lists and schedules. Digital transformation plans should align to the company’s overall strategic direction and goals.
So, what’s your goal? Are you trying to maximize margins? Create new revenue streams? Increase employee retention or safety? Once you have a handle on your biggest business needs, it’s easy to find and evaluate the right tools. List your company’s projects, then tie them to the most-productive tools.
Managing change
Each technology solution should have a business leader attached to it — not just an IT person. That keeps the solution aligned to the business case and other metrics of success, like cost and internal controls. A strong business case — and strong business leaders — can also support change management and user adoption.
Pull together “proof of concept” groups to assist with the rollouts. Recruit tech-savvy employees, plus outliers, like veteran workers or those who are frustrated with the status quo.
Communicate the benefits workers and users will experience, not just the business. Employees need to understand how the technology will improve their work lives — and feel like it’s worth it.
How Wipfli can help
Wipfli can help you tackle technology. Our professionals specialize in digital transformation, business strategy, labor planning and more specifically for construction firms. Together, we can build a better future.
Explore our Construction services to learn more, and subscribe to receive additional construction news and content in your inbox.
In the next article in our series on tackling disruption in the construction industry, we’ll cover how to tackle skyrocketing prices.
Related content: