Increase productivity by transforming your warehouse layout
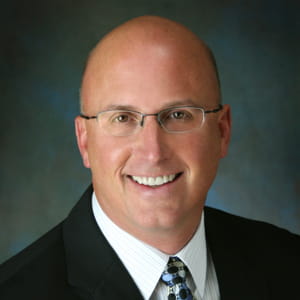
If you want to improve productivity in your distribution operation, evaluate your warehouse layout.
An efficient warehouse can help eliminate the wasted time and energy associated with search efforts and inefficient routes. It also prioritizes space, so that travel distances and product touches are minimized in the picking process.
To help your warehouse meet that standard, start by planning your picking, placement and communication methods.
Establish an ideal picking strategy
Planning your warehouse configuration starts with establishing a picking strategy. Defining how inventory will be located and moved can help you make more informed placement decisions.
There are multiple picking strategies, each with their own benefits depending on the type of operation:
- Single order: Pickers complete single orders by moving throughout the warehouse.
- Batch: Items are retrieved in bulk and used to fill multiple orders at consolidation.
- Multi-batch: Items for multiple orders are collected by pickers making a single pass through the warehouse. As items are picked, they are sorted into bins.
- Cluster: This strategy is like multi-batch. However, sorting is saved until after all the items are picked.
- Wave: Orders are organized into sets of waves. Pickers are then assigned to different waves, where they pick items and pass them forward to be consolidated.
- Zone: The warehouse is divided into zones with dedicated workers. Items are picked from each of these zones and then later consolidated.
The strategy that’s right for your operation depends on size. Medium-sized operations are usually more efficient with batch or multi-batch strategies, while larger warehouses may require wave and zone picking. For smaller operations, single order picking is often sufficient.
Optimize product placement
With product placement, planning is crucial. The right placement can help you optimize both operations and inventory, saving effort and costs.
It can even open new opportunities for improvements. For example, effective placement makes it easier to use an addressing system for items, which helps simplify tracking and auditing inventory.
To create an optimized warehouse configuration, consider these four key elements:
1. Location
When thinking of location, it’s helpful to consider how valuable space is in the warehouse.
The spaces closer to the dock are prime real estate, like beach front property. The space allows you to minimize picking efforts and travel times, so use it effectively by storing high-turn items or products that are difficult to move.
Towards the farther reaches of your warehouse, there are more open fields. These areas have a lot of space but are less valuable due to their distance from the dock. Use this space to store items that don’t require frequent access, such as those that have been discontinued or experience seasonal demand.
2. Communities
Items that have specific storage regulations, such as organic or frozen food items, are already sorted into communities. But for increased optimization, these communities can be broken down further.
Within communities, you can separate items into neighborhoods that have similar picking requirements or storage conventions, such as heavy and light items or pallets and cases.
Within those neighborhoods, you can divide items again into blocks. Blocks should be grouped based on model type or frequency.
3. Storage
Just like in a city, in a warehouse it’s cheaper to build up rather than build out a space.
Optimize the expensive real estate near the docks by using high-rise storage. Towers and similar options have a small footprint while allowing you to store a large amount of items.
Since open fields are less valuable, they’re a better space for items that can only be stored at floor level.
4. Routes
Routes represent a warehouse’s infrastructure: just like highways and streets, routes can be planned to provide faster, easier travel.
When planning, begin by establishing larger lanes that let traffic flow easily from the docks to the rest of the warehouse. Those highways should then be bisected by boulevards, allowing parallel travel from the dock for pickers. And smaller streets can be used to give easier access to high-turn products.
Be sure to also include specific addresses for each item and avoid creating dead ends or cul-de-sacs.
Implement communication solutions
An ideal warehouse layout strategy won’t be complete if it’s not paired with effective communication.
Relying on paper pick tickets or manual processes can slow down an operation and often lead to errors. Instead, leverage technology to increase accuracy and timeliness of picking and inventory information.
For greater efficiency, try solutions such as:
- Warehouse management systems: These systems can help automate certain inventory management tasks, and many already come integrated into NetSuite or other ERP software.
- Handheld devices: Mobile scanners and other handheld devices can communicate pick lists, inventory and layout information directly to pickers and even provide insight into picker performance. When used in conjunction with a barcode system, they can also help increase accuracy.
- Voice pick: With this technology, pickers wear headsets and receive verbal instructions on what to pick directly from operators. To convey real-time updates on inventory, operations usually include a visual status board.
- Pick to light: With this technology, LED lights are used to guide pickers to specific product locations.
- Mobile robots: Robots can save time and effort on repetitive, manual tasks such as moving items. Options such as automated guide vehicles can be used to move products throughout a warehouse and can even return items to their designated locations.
- Carousel systems: Carousels leverage inventory management software to make storing and picking smaller items more efficient. Items in these high-density storage towers can be individually barcoded, so all a picker needs to do is scan the right code and the tower will rotate to give them the corresponding item.
How Wipfli can help
Wipfli understands that each warehouse comes with its own unique challenges. Our experienced consultants are here to help you break them down and apply proven strategies to optimize your performance. Contact us today for more on how we can support your warehouse planning and implementation.
Sign up for more distribution industry information or continue reading: